By Gary Fleisher, the Modcoach
Modular construction is revolutionizing the way buildings come to life, promising significant gains in efficiency, sustainability, and cost-effectiveness. Despite these benefits, some modular factories are not immune to pitfalls that can derail their success. Challenges may arise from a variety of sources, impacting a factory’s trajectory.
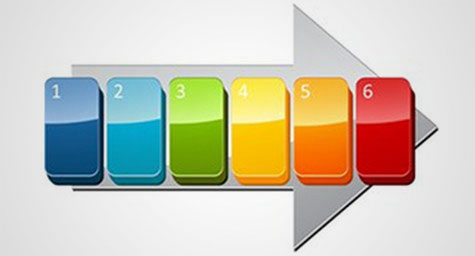
.
However, hope is not lost if your factory appears to be in jeopardy. With a strategic approach, you can navigate setbacks and guide your factory back to a path of success.
Step 1: Conduct a Thorough Project Audit
Identifying the root causes of the factory’s struggles is crucial. Undertake a meticulous audit covering all critical aspects:
Financial Review: Scrutinize the budgets, cash flow, and spending patterns. Look for areas where expenses have exceeded projections, and assess for any misallocation of resources that could be corrected.
Schedule Assessment: Examine the factory’s project timelines in detail to identify sources of delay. These could stem from supplier setbacks, workforce inefficiencies, or unforeseen logistical challenges.
Quality Control: Check that all modular units adhere to the predetermined quality standards. Issues like non-compliance with building codes or substandard workmanship can severely impede progress and need immediate attention.
Step 2: Enhance Communication
Frequent communication mishaps can be a major contributor to a factory’s difficulties. Strengthening communication channels can lead to more synchronized operations:
Regular Updates: Implement consistent and scheduled meetings with all team members, suppliers, and clients, to guarantee alignment and transparency.
Clear Documentation: Maintain comprehensive and up-to-date documentation of all project activities, changes, and decisions. This serves as a valuable reference that can aid in resolving disputes and tracking progress.
Feedback Loops: Set up efficient mechanisms for feedback to swiftly capture and address concerns from any involved party, thereby preventing small issues from escalating.
Step 3: Restructure Factory Management
Revising management may be necessary if there are indications of mismanagement:
Project Management Software: Investigate new management tools to monitor project milestones, manage budgets, and facilitate effective communication.
Professional Help: Engage a consultant with expertise in modular construction to provide specialized advice and direction.
Step 4: Renegotiate with Suppliers and Contractors
Revisiting negotiations with suppliers and contractors can provide opportunities for cost reduction and timeline acceleration:
Flexible Contracting: Collaborate with suppliers and contractors to devise flexible work arrangements that can adapt to changing your factory’s projects needs and timelines.
Step 5: Focus on Modular Integration
Proper integration of modular units is key to your factory’s projects success:
Site Preparation: Ensure that the construction site is optimally prepared for the timely arrival and installation of modular units.
Expert Installation Teams: Employ teams that specialize in modular construction to oversee the crucial stages of unit assembly and integration, ensuring a smooth process.
Step 6: Transparent Stakeholder Engagement
Maintaining stakeholder interest and trust is essential for ongoing support and funding:
Transparent Reporting: Regularly share detailed progress reports and recovery plans with all stakeholders to maintain transparency and confidence.
Navigating a troubled modular construction factory can indeed be daunting, yet it is not insurmountable. By taking decisive action to audit the factory, strengthen communication, restructure management, renegotiate contracts, ensure flawless modular integration, and actively engage stakeholders, you can reshape a faltering factory into a success story. Adaptability and determination are your best tools in overcoming the dynamic challenges of construction.
.
CLICK HERE TO READ THE APRIL ISSUE
.
Gary Fleisher is a renowned blogger and commentator on construction and housing trends, known for his insightful analysis of the industry.